Frank Lavety
General Manager, Kandou
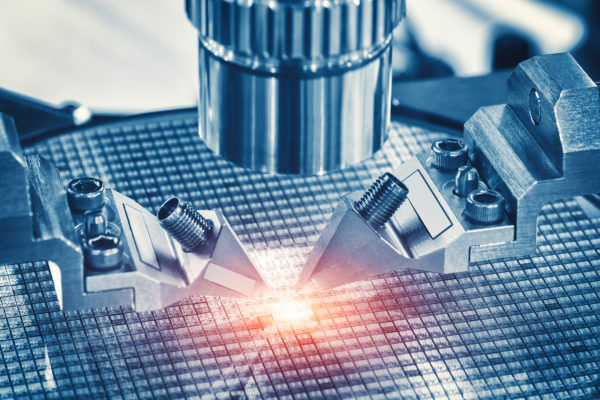
Close up of examining of test sample of microchip transistor under the microscope in laboratory. Equipment for testing microchips. Automation of production. Manufacturing of microchips.
COVID was a catastrophic event that created a rare combination of challenges for the semiconductor industry –– demand for electronic devices to support working from home, supply chain disruption, production line slowdowns and long delivery delays of finished products to end users. Lean manufacturing, otherwise known as Just-in-Time manufacturing, was in peril.
The demise of Just-in-Time (JIT) manufacturing, however, has been greatly exaggerated. Like everything in the semiconductor industry, economy slumps and supply and demand woes are cyclical. This cycle will smooth out eventually and may bring some systematic modifications. It happened in the early 2000s when the dotcom bubble burst and again in 2008 with the stock market crash. It was 12 years of normal behavior before COVID and the pressure on the supply chain as demand grew for consumer electronics or anything associated with working from home or home entertainment. The result was extraordinary.
To put the COVID phenomenon into perspective, think of it as a reset. So was the dotcom era, though it wasn’t all about semiconductors. Companies had valuations that were ridiculous in 2000 and investors saw it. Then in 2008, I was in a highly analog/mixed-signal world with a glut in capacity and realized segments of the business could be impacted by investments. Resets in both cases.
Several months into COVID in 2020, there was a realization that some aspects of the supply chain were a little too lean and there was a push for more capacity, which is what happened. Increasing capacity is a long-term investment, then demand smooths and it goes back to running a normal rate.
What’s happening now is a burndown of inventory. PC OEMs are looking at their inventory after having to consume a large amount of it to make sure that they had supply during COVID. It’s become a double boom of problems because of the global recession and the rise in interest rates to counteract inflation. Although the dollar is strong, companies are now reporting drops in sales and revenue. Some have lost market share and some are holding off on pulling inventory so that their financials look as strong as possible.
As soon as a company takes inventory, inventory converts to cash and it’s no longer a flexible asset. It becomes a fixed asset. It’s fixed through either a product or an application, and therefore, the burden of that cash is now on the purchaser. Whereas JIT is making sure that the burden of the cash is on the supplier, and the supplier makes the product available to the purchaser as soon as it needs it. It’s about squeezing the cost back down the supply chain. As part of that chain in a supply chain, semiconductor companies do that with their own suppliers and purchase wafers within the lead time.
Planning and accurate forecasting are key aspects of JIT, the well-honed management system refined in Japan in the 1970s to align orders from suppliers directly with production schedules. JIT was first adopted by Toyota then moved to Fremont, Calif., with automotive and swept through the semiconductor industry. JIT is as important a methodology for increasing efficiency, reducing inventory cost and waste and accurately forecasting demand as it was when I first started my career and researched it as part of my MBA thesis.
At the time, I set up manufacturing warehouses for a company that produced an audio chip for a well-known consumer electronics company. My job was to work with its subcontractors or ODMs. I used the Kanban scheduling system alongside JIT to manage overcapacity. An ODM would pull whatever chips it needed directly onto the line, and then send a signal to us to show that it pulled the chips and we would invoice the customer. That’s still the way systems are built.
The cycle begins with the sales organization and its sales funnel. Manufacturing executives look at it to learn as much as possible about the dynamics of the customer base and work with sales on demand and operations planning. With that intelligence, manufacturing can better understand a customer’s financials and are better able to predict what their demand signals are going to be, then relay that into supply chain planning. The objective is to strip out as much waste in that chain. If a wafer takes 14 weeks, for example, they plan for that with little buffer. If assembly and test take four weeks, it’s an 18-week cycle. That’s considered the pipeline and manufacturing executives want to make sure that that pipeline is as thin as possible with few chunks in it.
It’s like the python eating the watermelon –– no visible sign of that watermelon. Manufacturing executives want to make sure the whole supply chain is running smoothly. Companies use enterprise planning systems to identify demand signals. In our case, Kandou gets automated weekly demand signals from customers. The reports include whatever buffer customers want to hold in, giving predictability on a week-by-week basis as to what we should be shipping. We need to have that inventory available.
JIT is more than enterprise-wide planning software. An equally important component is partnerships and open communications. The Oxford dictionary definition of partnership can be different when it pertains to business partnership where a smaller company will get a purchase order as long as it does everything the larger company demands. Take the example of an OEM that knows how many PCs are in stock throughout its channel. It knows what the next generation is going to be and consumer interest. It knows the next use case and how it’s going to stimulate demand. It also understands the burn-off rates in each one of those related supply chains but may not share that information with its partners. That’s why customers and suppliers need to communicate and work together cooperatively to make sure that waste is squeezed out of the entire system. It can’t be that a big brand demands that its small supplier hold inventory for them. They need to look at their suppliers as partners so they can openly talk about demand signals and share intelligence.
Conclusion
JIT worked through COVID until demand outstripped supply. Short-term, it may take a hybrid approach while there’s an overstock of inventory as buy-ahead and new capacity come on-line. It will smooth out and there will be an adjustment and an element of burn off. Once the semiconductor industry gets through the burn off, there will be a cycle where the industry has more capacity installed, and therefore, the value chain and the supply chain will adjust based on where the inventory is.
A good example is a PC that costs $1,000. Consumers may change their buying behaviors because that $1,000 bracket is considered too high. It needs to change. It’s a bit like price elasticity that changes based on economic factors. That will re-adjust and fix itself, and there will be a glut of capacity and pricing will need to adjust because consumers will be stimulated to buy products by pricing as well as feature differentiation and improved performance like USB4.
As analysts of the future look back on COVID, they will agree that JIT worked until extraordinary events changed the game and we had to reset. JIT isn’t a fad. It’s a way of life for manufacturers.
About Frank Lavety
Frank Lavety is General Manager at Kandou and is responsible for building Kandou’s fabless manufacturing operations and leading engineering, manufacturing, and the commercialization of Kandou’s products. Previously, Lavety worked for Wolfson Microelectronics, a fabless semiconductor startup and the medical device manufacturer Haemonetics Corporation. While at Wolfson, he established manufacturing capabilities and led a team capable of shipping billions of mixed signal ICs to the world’s largest consumer electronics brands, establishing Wolfson as a world leading brand in audio technologies. Lavety holds a Bachelors degree with Honors and an MBA from University of Strathclyde in Glasgow, Scotland.